Great results for customer after Satake sorter added to process
Posted on Mon 16th Mar 2020
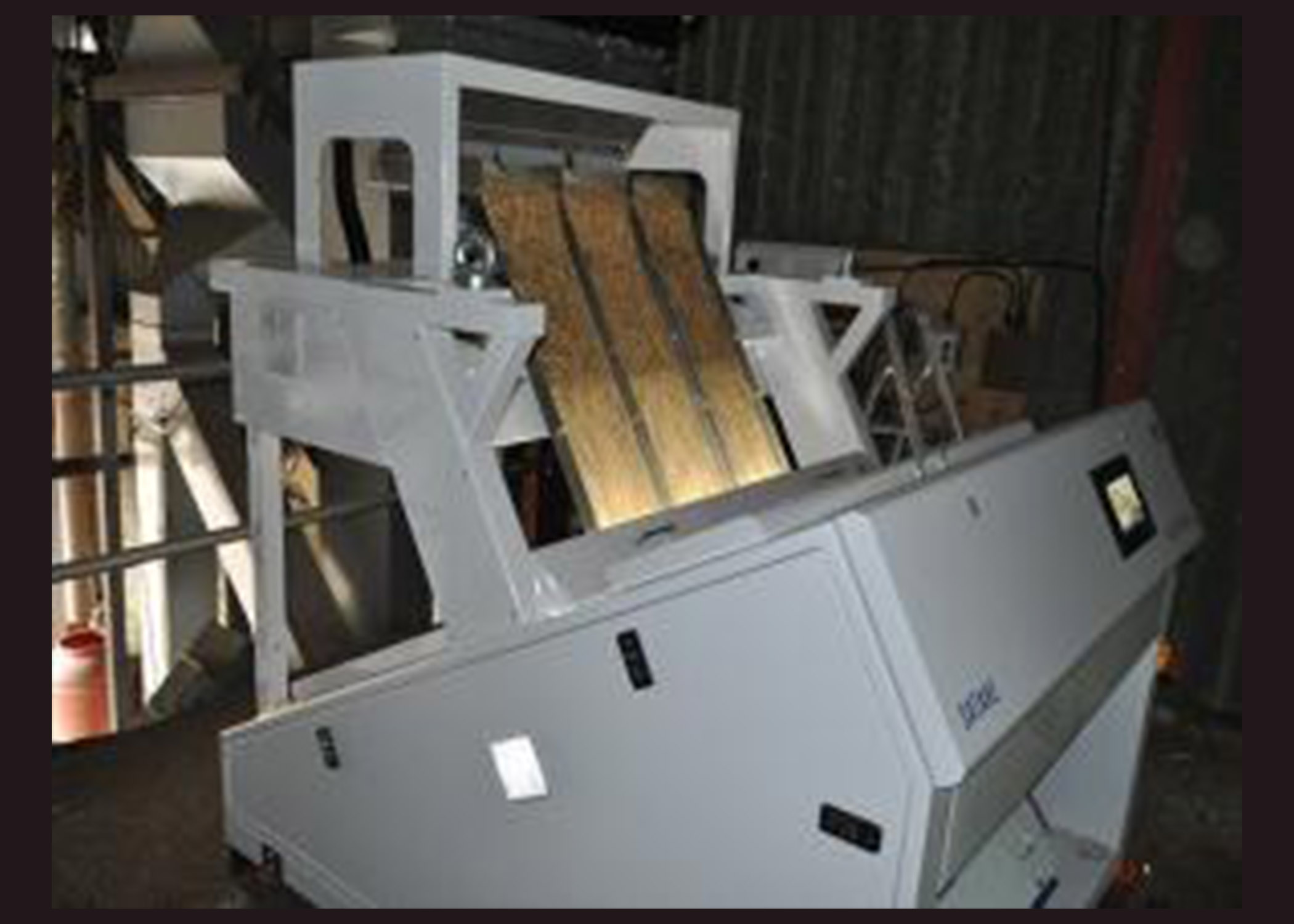
VIDEO: J F Marsh Complete Full Refurbishment with Perry of Oakley and Satake
Roger & Neil Marsh, a father and son from J.F Marsh and Son, based on the Isle of Sheppey, have recently completed a full refurbishment of their grain handling, cleaning & drying equipment. With the help of Perry and Mike Bartter Systems Ltd., the 4th generation, family run farm have increased and improved their drying capacity and the quality of their grain, enabling them to sell their product into more sought after markets at a higher premium.
In the 1970 / 1980s Roger Marsh had a 19 foot diameter Shivvers drier installed, which at the time was a top of the range drier that was capable of drying 4tph (100 tonne per day) if the ambient conditions were correct. They had used various handling equipment manufacturers, but favoured the Perry equipment for ease of use and reliability.
After 35+ years of service, the drier broke down on three separate occasions during one harvest. Each occasion costed J.F Marsh & Son in excess of a week’s worth of drying time and it was at that point they decided to upgrade the machinery. They chose to upgrade to a Perry 26tph continuous mixed flow drier with the Light Grain & Chaff Recovery System (LGCRS) and Perry CentriKleens fitted as optional extras.
The Light Grain & Chaff Recovery System is a pneumatically operated system that is installed at the base of the exhaust plenum. It has been designed to help reduce the build-up of dust, chaff & seeds in the plenum by periodically discharging any product that may have been drawn from the grain column and return it back into the main grain flow. The Light Grain & Chaff Recovery System (LGCRS) removes the need to clean out light grains and chaff from the drier exhaust plenum as often, saving time and effort.
The Perry CentriKleen is the biggest step forward in allowing farms to cost effectively collect the dust emitted by their grain drier and also presents the most cost effective retrofit device for existing driers on the market. The Perry CentriKleen is the simple solution to your drier’s dust & chaff problems, helping to keep roofs and yards clean.
To accompany the drier, the Marsh family installed 60tph Perry handling equipment with several store conveyors (including a curved combination with a mechanical reception hopper), a double lift belt & bucket elevator, an aspirator pre-cleaner and an auger. This equipment allows the farms wheat, oil seed rape, beans & barley to be delivered to the 4,000 tonnes of stores that are a mixture of bin storage and floor stores. Some of the stores date back to the 1960’s.
With the export market reducing, Neil Marsh decided to increase the volume of grain he sold into the UK market. He quickly found that the UK mills were more stringent with their regulations governing grain quality. He was quoted £25,000 per harvest to clean the grain to the required standard. This led to their most recent purchase, a Satake Optical Sorter where Perry acted as a Satake dealer. In only three seasons the cost of the Optical Sorter would be justified.
The grain will pass through the Satake a total of three times. The first will be at its maximum throughput of 9tph, allowing the impurities to be removed from the bulk of the grain. The rejected grain will then be run through again at a slower pace, allowing for more of the good grain to be saved. They will then run the rejected grain through once more, specifically targeting the ergot within the crop. This will allow them to sell the ergot into the alternative medicines market, meaning a product that would normally have been burned as refuse could now potentially provide them with an additional income and entry into additional markets.
Mr Marsh commented that he was surprised at how simple the whole installation had been. He was very impressed with the 60tph rated Perry machines being able to so easily adapt to feeding the 9tph Satake using just simple inverters.
The whole system is controlled with Perry’s PLC plant control panel. It is a 12” touch screen panel which is designed and programmed by Perry’s experienced engineers. The ease of use of the PLC panel is always one of the first things mentioned by Perry customers, and it is no different with the Marsh’s.
Neil & Roger Marsh said: “We are really happy with the Perry equipment, we would recommend it. Having built the drier ourselves we can vouch for the simplicity of the Perry equipment, but it is also built to a great standard, making it reliable. We are really happy with our new plant. We know & trust the Perry machines and have found their staff to be helpful, friendly, knowledgeable who aim to please.”
Published by firstinternet
Share this article on: